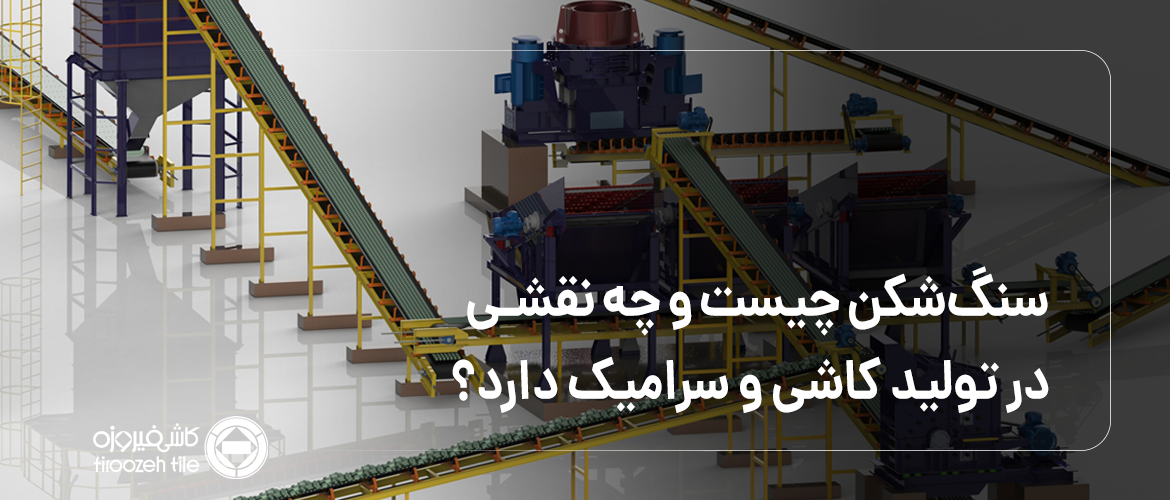
سنگشکن چیست و چه نقشی در تولید کاشی و سرامیک دارد؟
در فرآیند تولید کاشی و سرامیک، آمادهسازی مواد اولیه یکی از مراحل حیاتی است که تأثیر مستقیمی بر کیفیت محصول نهایی دارد. سنگهای استخراجشده از معادن دارای ابعاد و سختیهای مختلفی هستند و برای استفاده در فرآیند تولید، باید به اندازههای مناسب خرد شوند. این وظیفه بر عهده واحد سنگشکن در کارخانه است که با استفاده از دستگاههای مختلف سنگ شکنی، مواد اولیه را به ابعاد استاندارد تبدیل میکند. در این مقاله به معرفی انواع دستگاه سنگ شکن، عملکرد این دستگاه و اهمیت آن را در صنعت کاشی و سرامیک بررسی خواهیم کرد.
سختی مواد اولیه و ضرورت خردایش آن با دستگاه سنگ شکن
مواد اولیه متعددی در صنعت کاشی و سرامیک به کار میروند که هر یک ویژگیهای خاص خود را دارند. در این میان، موادی مانند فلدسپار و کائولن از جمله موادی هستند که سختی بالاتری نسبت به برخی دیگر از ترکیبات مصرفی دارند. سختی این مواد معمولاً بین ۵ تا ۶.۵ در مقیاس موس است. مقیاس موس معیاری برای سنجش سختی مواد است که از ۰ (گرافیت، نرمترین ماده) تا ۱۰ (الماس، سختترین ماده) درجهبندی شده است. موادی که سختی آنها بیش از ۵ موس باشد، پیش از استفاده در فرآیند تولید، باید خردایش شوند. برخی کارخانهها دارای واحد سنگشکن داخلی هستند، در حالی که برخی دیگر مواد اولیه را بهصورت خردشده (با حداکثر اندازه ۱ تا ۲ سانتیمتر) از معادن دریافت میکنند.
فرآیند سنگشکنی و چرخه خردایش
مواد اولیه پس از استخراج از معادن مختلف، به دپوی سالانه کارخانه منتقل میشوند. این مواد ممکن است ابعادی تا 40 یا 50 سانتیمتر داشته باشند و در اولین مرحله از تولید باید به قطعاتی کوچکتر تبدیل شوند تا در فرآیند دوغابسازی قابلاستفاده باشند.
ابتدا برنامه روزانه تولید توسط واحد صنایع تنظیم شده و به سرپرست واحد سنگشکن ابلاغ میشود. سپس، مواد اولیه مشخصشده به واحد سنگشکن انتقالیافته و داخل قیف، تخلیه میشوند. در این مرحله، مواد با ابعاد کمتر از 5 سانتیمتر از طریق سرند عبور کرده و مواد بزرگتر برای خردایش اولیه به سنگشکن فکی هدایت میشوند. پس از عبور از سنگشکن فکی، مواد وارد سنگشکن چکشی شده و در نهایت از طریق سرند دو طبقه، مواد با ابعاد مناسب جدا شده و به سیلوهای روزانه انتقال مییابند.
در صورتی که مواد خروجی از آخرین سنگ شکن هنوز به ابعاد مناسب نرسیده باشند، مجدداً به چرخه خردایش بازگردانده میشوند و این روند تا زمانی که همه مواد به اندازه استاندارد برسند، ادامه پیدا خواهد کرد.
انواع سنگشکنها در صنعت کاشی و سرامیک
- سنگشکن فکی: این نوع سنگشکن دارای دو فک ثابت و متحرک است که مواد را بین خود قرار داده و با اعمال فشار خرد میکند. این دستگاه برای خردایش اولیه مواد سخت بسیار مناسب است.
- سنگشکن چکشی: شامل یک سندان و یک روتور متحرک از جنس سیلیکون کارباید است. در این سنگشکن، مواد پس از ضربههای متوالی به قطعات کوچکتری تبدیل میشوند.
- سنگشکن بارمک: این نوع سنگشکن بر اساس نیروی گریز از مرکز عمل کرده و از جمله سنگشکنهای عمودی محسوب میشود. بارمک دارای هزینه نگهداری پایین و بازدهی بالایی در خردایش سنگهای نرم است و در آخرین مرحله خردایش از آن استفاده میشود.
چالشهای واحد سنگشکن
فرآیند سنگشکنی در کارخانههای تولید کاشی و سرامیک همواره با چالشهایی همراه است که میتوانند منجر به توقف تولید و کاهش بهرهوری شوند:
- ورود مواد با رطوبت بالا به سنگشکن فکی میتواند منجر به ازکارافتادن فک، سوختن موتور و یا فیوز دستگاه شود.
- در صورت گیر کردن مواد در سنگشکن چکشی، نیاز به تخلیه دستی و باز کردن دیواره دستگاه است که فرایند را دشوارتر میکند.
- فشار زیاد روی تسمهها در اثر عدم تخلیه بهموقع، میتواند باعث پاره شدن تسمهها و سوختن فیوزهای موتور شود.
اهمیت سنگشکن در صنعت سرامیک
سنگشکن نقش بسیار مهمی در بهینهسازی فرآیند تولید کاشی و سرامیک دارد. برخی از مهمترین دلایل اهمیت این واحد عبارتند از:
۱. لزوم خردایش مواد اولیه
مواد اولیهای مانند فلدسپار و کائولن دارای سختی بالایی هستند و اگر بدون خردایش وارد بالمیل شوند، زمان سایش بهطور قابلتوجهی افزایش مییابد. این مسئله باعث میشود که برخی مواد بیش از حد ساییده شوند و ترکیب نهایی دچار تغییراتی نامطلوب شود. بهطور کلی:
- اگر مواد اولیه بیش از حد درشت باشند، مدتزمان سایش در بالمیل افزایش مییابد (گاهی این زمان تا دو یا سه برابر افزایش خواهد یافت.
- ساییدگی بیشازحد برخی مواد، باعث بر هم خوردن دانهبندی و کاهش کیفیت سرامیک میشود.
بنابراین، سنگشکن با رساندن مواد به ابعاد مناسب، موجب افزایش راندمان بالمیل و بهبود کیفیت نهایی محصول میشود.
۲. جنس بدنه سنگشکن و تأثیر آن بر ترکیب مواد
اگر سنگشکن از آهن یا فولاد ساخته شده باشد، با گذشت زمان دچار سایش شده و ذرات فلزی آن وارد ترکیب مواد اولیه میشوند. وجود آهن در ترکیب سرامیک نامطلوب است، به همین دلیل تا حد امکان باید از ورود این فلز جلوگیری کرد. برای این منظور:
- در مسیر انتقال مواد، مگنتهایی قرار داده میشود تا ذرات آهن جدا شوند.
- استفاده از سنگشکنهای ساختهشده از سیلیکون کارباید پیشنهاد میشود، زیرا این ماده در برابر سایش مقاومت بالایی دارد و ناخالصی کمتری به فرمولاسیون محصول وارد میکند. البته سیلیکون کارباید نیز بهمرور ساییده میشود، اما میزان آن در مقایسه با آهن و فولاد بسیار کمتر است.
در یک نگاه
واحد سنگشکن یکی از بخشهای کلیدی در صنعت کاشی و سرامیک است که وظیفه خردایش مواد اولیه و آمادهسازی آنها برای فرآیند تولید را بر عهده دارد. انتخاب صحیح نوع سنگشکن، مدیریت چالشهای عملیاتی و کنترل کیفیت مواد خروجی از جمله مواردی است که تأثیر مستقیمی بر عملکرد و بهرهوری کارخانههای تولید کاشی و سرامیک دارد. علاوه بر این، توجه به جنس قطعات سنگشکن و جلوگیری از ورود ناخالصیهای نامطلوب به مواد اولیه میتواند کیفیت نهایی کاشی و سرامیک را تضمین کند. با استفاده از تجهیزات مناسب و رعایت استانداردهای عملیاتی، میتوان این فرآیند را بهینه کرده و کیفیت محصولات نهایی را افزایش داد.
برای مشاهده مستند واحد سنگ شکن در کارخانه کاشی فیروزه کلیک کنید.